Big Sky Packaging: Pioneering Ultrasonic Welding Innovation for Over 20 Years!
- 10 July, 2024
- 4 minutes
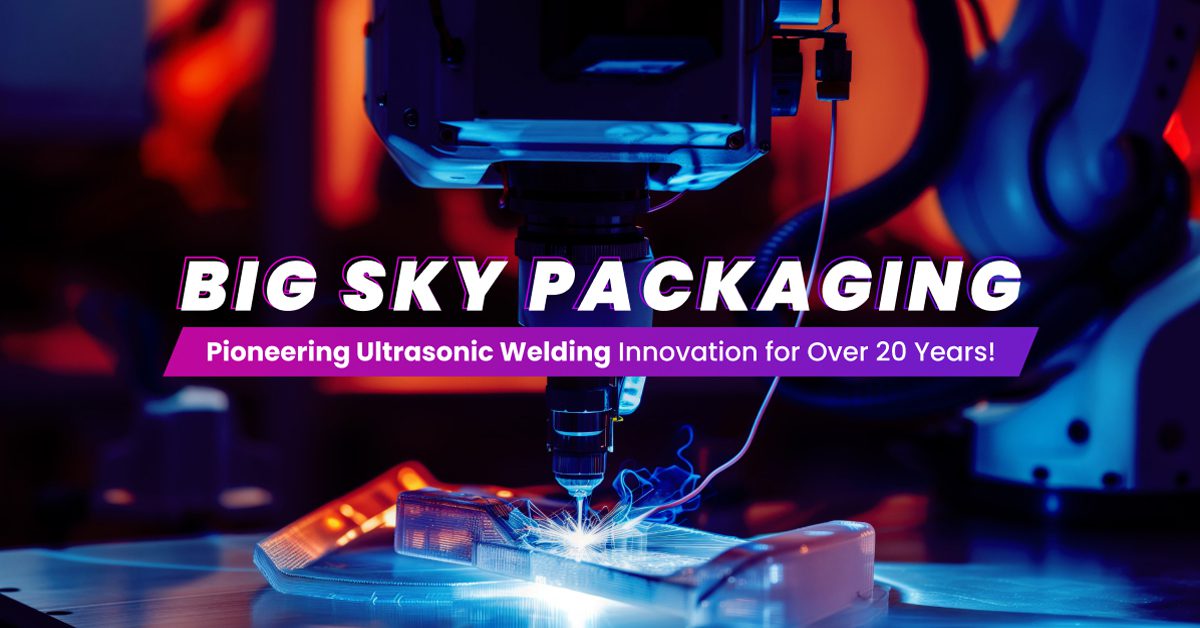
In a world where sustainability meets cutting-edge technology, Big Sky Packaging stands as a pioneer with over 20 years of pioneering ultrasonic welding innovation. This revolutionary technique eliminates the need for adhesives, dramatically reducing waste and emissions while enhancing product integrity. Imagine packaging that is not only more robust and secure but also environmentally friendly and energy-efficient.
We have harnessed this powerful technology to provide seamless, sustainable solutions that set new industry standards
The Evolution of Ultrasonic Welding
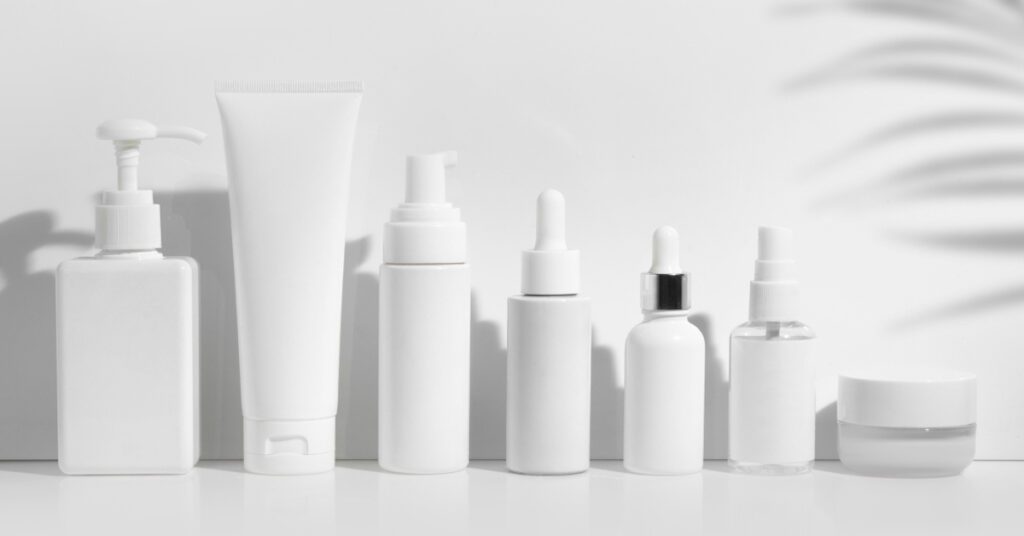
Ultrasonic welding is a process where high-frequency ultrasonic acoustic vibrations are applied to workpieces being held together under pressure to create a solid-state weld. This technique is particularly effective for joining dissimilar materials and intricate assemblies, making it a preferred choice in various industries, including automotive, electronics, and packaging.
Big Sky Packaging has harnessed the power of ultrasonic welding to provide seamless and reliable bonding of plastic components. Unlike traditional methods that rely on adhesives or mechanical fasteners, ultrasonic welding offers a cleaner, more efficient solution. This method not only enhances the structural integrity of the final product but also significantly reduces environmental impact by eliminating the need for chemical adhesives.
Commitment to Sustainability

Sustainability is a core value at Big Sky Packaging, driving every aspect of our operations. The company’s ultrasonic welding technology aligns perfectly with this commitment by minimizing waste, reducing energy consumption, and avoiding harmful emissions associated with traditional bonding methods.
We belive that our mission is to provide packaging solutions that not only meet our clients’ needs but also contribute positively to the environment. Ultrasonic welding is a prime example of how innovative technology can drive sustainability in the packaging industry.
Benefits of Ultrasonic Welding
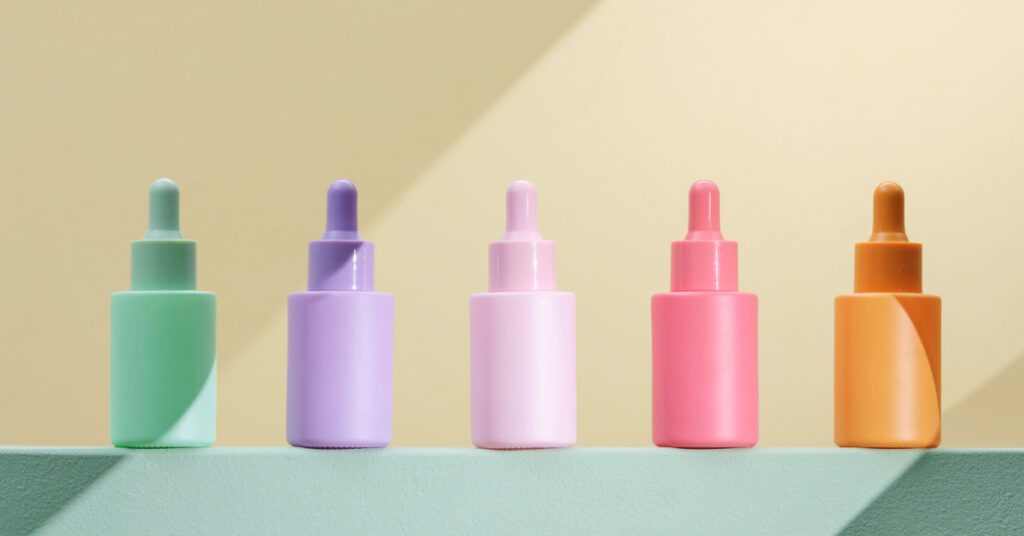
Environmental Impact Reduction: By eliminating the need for adhesives, ultrasonic welding drastically reduces waste and harmful emissions, lowering the carbon footprint of the manufacturing process.
Energy Efficiency: The process requires less energy compared to conventional methods, contributing to overall energy savings and reducing greenhouse gas emissions.
Resource Conservation: Products created using ultrasonic welding are more durable and less prone to damage over time, which reduces the need for replacements and conserves resources.
Production Efficiency: Ultrasonic welding streamlines the assembly process, improving production efficiency and potentially leading to long-term cost savings.
Industry Applications and Impact
Big Sky Packaging’s ultrasonic welding solutions have been widely adopted across various industries. In the beauty and personal care sector, for instance, the precision and reliability of ultrasonic welding ensure that packaging remains secure and tamper-proof, enhancing product safety and consumer trust.
In the electronics industry, ultrasonic welding is used to create strong, conductive bonds between components, ensuring the longevity and performance of electronic devices. The automotive industry benefits from the technique’s ability to join dissimilar materials, crucial for lightweight and improving fuel efficiency.
A Future-Oriented Approach
As industries increasingly prioritize sustainability, Big Sky Packaging’s pioneering approach to ultrasonic welding positions them as a forward-thinking leader. The company continually invests in research and development to refine its techniques and explore new applications, ensuring they remain at the cutting edge of packaging innovation.
“We believe that the future of packaging lies in sustainable practices and innovative technologies,” said the spokesperson. “Our commitment to ultrasonic welding is a testament to our dedication to these principles.”
Client Success Stories
Several high-profile clients have benefitted from Big Sky Packaging’s ultrasonic welding expertise. By partnering with the company, these clients have been able to achieve their sustainability goals while maintaining high standards of product quality and reliability.
One notable success story involves a leading cosmetics brand that sought a more eco-friendly packaging solution. By switching to ultrasonic welding, the brand was able to eliminate the use of harmful adhesives, reduce packaging waste, and improve the overall durability of their products. This move not only enhanced the brand’s environmental credentials but also resonated positively with eco-conscious consumers.
Looking Ahead
Big Sky Packaging is committed to pushing the boundaries of what is possible with ultrasonic welding. The company is exploring new materials and applications, aiming to broaden the scope of this technology and its benefits. By fostering a culture of innovation and sustainability, Big Sky Packaging is well-positioned to lead the packaging industry into a greener, more efficient future.